我今年出來也是覺得做技術(shù)的不容易,想要把工作和技術(shù)落到實處,將好的記錄和提高習(xí)慣和做項目巷戰(zhàn)的技巧結(jié)合起來,培養(yǎng)技術(shù)團隊這個事情就需要建立一個簡要的技術(shù)系統(tǒng)框架。我現(xiàn)在第一要緊的是圍繞著電池系統(tǒng)里面高低壓配電系統(tǒng)建立一個初步的體系。
如下圖所示,線束其實分成兩個部分,物理上連接和電氣連接保護兩個大的方面。在客戶輸入方面主要包括:
客戶要求:這里主要是相關(guān)部件的實際聯(lián)通需求,正常的企業(yè)在ECU層面用軟硬件接口定義物理連接,在ECU線束連接中采用ICD接口定義表格來做。實際在收集通常定義之后,展開設(shè)計之前,最主要是收集多少個連接點,以及這些連接點所需要承載的電流。
公司要求:每個公司在歷史上會在很多個環(huán)節(jié)提出不少的標(biāo)準(zhǔn),選擇依據(jù)和推薦的部件清單。在實際功能層面之外,比如整個大的系統(tǒng)要求上對聯(lián)通系統(tǒng)是有要求的,這塊往往是通過類似短路保護性能、EMC抗擾度要求等等比較系統(tǒng)的內(nèi)容來傳遞的。接到不同的項目之后,實際需要根據(jù)橫向項目對比來評估每個項目滿足企業(yè)標(biāo)準(zhǔn)和企業(yè)項目系統(tǒng)規(guī)范的實際難度。
法規(guī)要求:在新能源汽車?yán)锩妫瑖鴥?nèi)做了大量的GB和行業(yè)標(biāo)準(zhǔn)?,F(xiàn)在已經(jīng)進入高壓電纜設(shè)計要求了,這塊的輸入是需要確認和深究的。
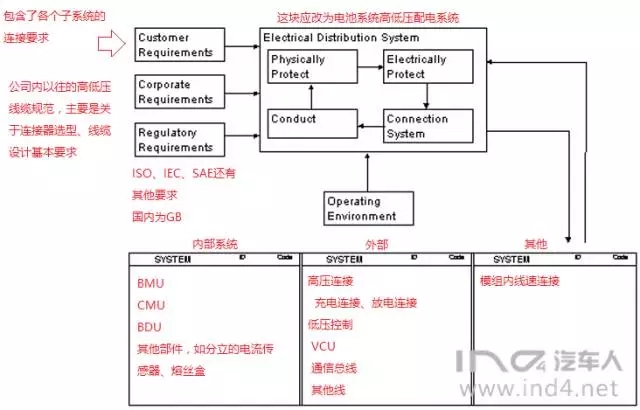
圖1 根據(jù)低壓配電系統(tǒng)更改而來的電池系統(tǒng)配電要求
由于很多的線束設(shè)計,是建立在實現(xiàn)導(dǎo)通性為目的的,所以從整個項目走下來,設(shè)計內(nèi)容和設(shè)計要求并不多,倒是有不斷修修補補的Issue List。每個問題從發(fā)生到解決,留給后面的余地并沒有那么多,有時候由于供應(yīng)商、自身組裝和項目的重要性等等,一些可以深究的問題并沒有貫徹下去。我個人的看法還是從以下的幾點來看問題:
建立一份設(shè)計需求和設(shè)計考慮清單:如下表所示,從整車的設(shè)計考慮入手,每個車企都會有較為完整的設(shè)計要求,把這份材料遷移到電池系統(tǒng)里面,把每個要求通過初步的判斷來確認是否有合理性,如已經(jīng)不需要了則進行省略
由于高壓的原因,使得高壓線路和低壓線路進行了分離,區(qū)別于傳統(tǒng)的線束設(shè)計,由于電壓所引起的問題就迎面而來
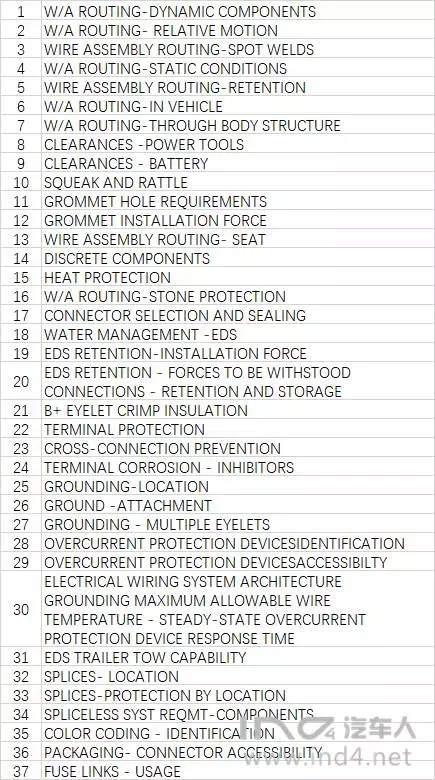
表 1 傳統(tǒng)車EDS線束配電問題,設(shè)計考慮問題清單
我這里舉一個例子,也是前陣子小兄弟盯著我問,采樣線連接器相鄰引腳的壓差怎么布置。這個原始的問題如下:
問題:在不同的電池項目里面,需要考慮采樣線,采用集中式處理的時候,采樣線束處理在一起之后通過連接器處理,處理信號間距主要是在連接器上面。而在分布式系統(tǒng)的時候,需要考慮FPC/PCB連接線和連接器,在不同配置的時候,由于連接器的限制和FPC的限制,整個引腳的排布和間距如何控制?
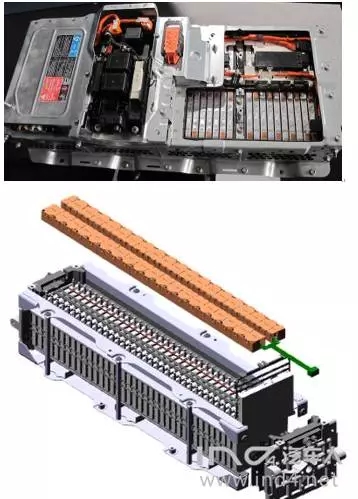
圖2 HEV 電池模組
在我之前很早的博客里面,在傳統(tǒng)的ECU設(shè)計接插件的時候要注意,引腳相鄰距離,在不斷的插拔過程中,引腳可能彎曲和退針,這樣會引起嚴(yán)重的短路事故,這是不被允許的。一般在選用連接器的時候,傳統(tǒng)汽車級別的額定電壓(工作電壓)(Rated Voltage ) ,都是合規(guī)的,推薦的最高工作電壓,主要取決于所使用的絕緣材料,接觸對之間的間距大小。某些元件或裝置在低于其額定電壓時,可能不能完成其應(yīng)有的功能,連接器在低于額定電壓下都能正常工作。如果寫了一個40V,我用在了需要聯(lián)通多片電芯的設(shè)計上,這個事如何考慮?
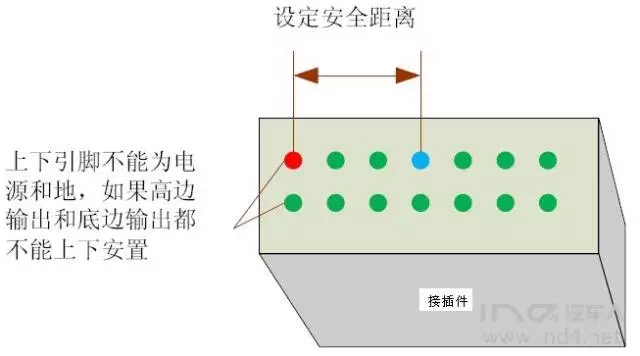
圖3 12V ECU引腳排布
整個耐環(huán)境特性,如果沒考慮好直接用,往往也會出現(xiàn)極端的情況發(fā)生
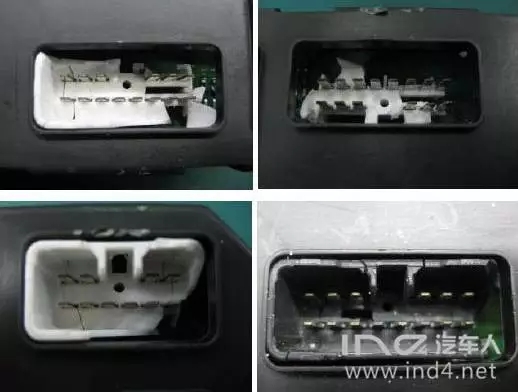
在我們的不同組成的模組里面,這個電壓可能極端的時候,給拉到60V以上,這個排布和電氣保護考慮,就比之前的設(shè)計要多做很多的思慮了。
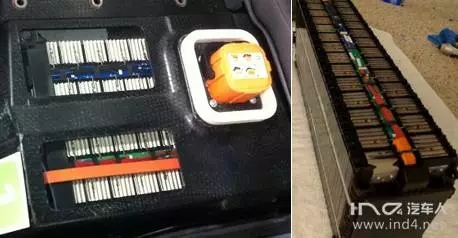
圖4 模組配置在PHEV電壓可能會很高
開個頭,建立技術(shù)體系的事,我也在路上。
171 閱讀